Fly ash handling systems
EWB ash handling and other bulk material handling technologies can cover all requirements.
EWB Ltd. has developed different kind of Ash Handling technologies suitable for Pulverized Coal Fired Boiler as well as Fluid Bed Boiler application.
The selected technology we are offering for the collection, transportation and storing of the ash depends on many factors such as:
- Type of boiler
- Numbers of Units
- Size of the Units
- Type of coal or other fuel
- Quantity of ash
- Particle size and chemical composition of ash
- Numbers of ESP hoppers
- Plant arrangement
- Requirements against ash disposal side
- Distance of ash disposal area
- Silo distance from the Units
- Special requirement e.g. utilization of fly ash
For the fly ash collection and transportation we can design and supply different pneumatic transportation system such as:
- Airslide-Airlift system
- Dense phase pneumatic transport
- Vacuum type pneumatic transport
- Mechanical ash collection & transport
- High concentration ash slurry disposal system
- Positive pressure lean phase pneumatic transport.
- Silo technologies
We offer always the more suitable technology or their combination depending on factors listed above.
Airslide-airlift systems
The Airslide-Airlift material transport is usually used together.
It is a simple and well proven design and suitable to transport large quantities for short distances. Typical application when the fly ash has to be collected from the large number of ESP hoppers and has to be transported into a near-by fly ash storage silo.
Airslide channel
Technical parameters:
- Standard transport capacity: 1 - 500 t/h
- Standard transport distance: 10 - 200 m
- Specific air demand: 100 - 500 m3/h/m2
Advantages of the application:
Low investment and operating costs, operational safety, simplicity, flexibility and high transport capacity depending on channel size. It has no moving part and transports the material with low speed, in a protecting operating mode. There is a stable working point in wide range according to change of the loading, that is, the same channel is able to operate even for a considerably changed material quantities.
The most frequent application fields:
- fly ash transport systems of power stations
- aeration and discharge of silos
- transportation of bulk, fluidizable materials in industries such as:
- cement works
- lime plants
- chemical industry
Airlift
The Airlift is used for vertical transportation of fly ash, cement and fine-grained materials.
Technical parameters
- Standard transport capacity: 10 - 150 t/h
- Standard vertical lifting height: 10 - 80 m
Advantages of the application:
The Airlift has simple structural constructions, contains no moving part, its operating cost is low and can be operated safety in wide operating range. The airlift has a stable working point and the equipment is self-adjusting.
The most frequent application fields:
In fly ash handling systems, cement works & chemical plants vertical transportation of bulk material in large quantities into large-size silos, intermediate storage tanks.
The fly ash collection with airslide can be combined with dense phase transport. EWB offer this version for big units (large Nos. of ESP hoppers) when the fly ash storage silo is far from ESP.
The fly ash collected from ESP hoppers via airslide is collected in a small transfer bin. Under the bin transport vessel is put and the material is conveyed by dense phase transportation modus to the storage silo which can be located up to 1500 m far away from the ESP areas.
EWB has numerous references for this arrangement with very good experience.
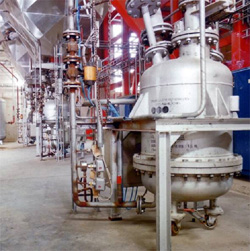 Dense phase pneumatic transport
In the last 15-20 years it is a trend world-wide to use dense phase pneumatic conveying for fly ash collection and transportation. EWB has developed its own dense phase design and we have a well proven technology with many references.
Why dense phase?
- High material to air ratio, big quantities can be transported for long distances with less air.
- Due to lower velocity less wear
- Long conveying distance in one stage up to 1500 m
- No storage in ESP hoppers, fly ash is collected in the transporting vessels
- No sucking of flue gas, therefore danger of condensation is minimized while filling and during conveying no danger of plugging
- Due to dense phase smaller transport pipes required, consequently less structure and erection works
- Lower power consumption compared to other methods.
Technical description of the system:
Depending on the UNIT size, the Nos. of ESP hoppers, ash quantities and plant arrangement (storage silo distance from ESP area) we can offer different arrangement most suitable and economical for the actual requirements.
Typical arrangements we are usually offering:
- Direct, multi dense phase transport from each ESP hoppers to storage silo. This simple solution can be used for silo distance up to 500 m. For this direct transportation system we have developed pair and group operation of the transport vessels. It means that up to 4 Nos. of vessels can be operated simultaneously is such a way that the transport vessels are working onto one common delivery pipeline. It results simpler and maintenance friendly operation since the number of valves is reduced. This arrangement is usually recommended under the 3rd , 4th and 5th row of the E-precipitator hoppers.
- Two stage dense phase transport. In the first stage the fly ash is collected by individual vessels into a transfer bin and the long distance transportation from transfer bin to storage silo (up to 1500 m distance) is made by Jumbo transport vessel.
- Two stage transportation, where the fly ash collection is done by airslide, mechanical or vacuum system and the long distance transport by single Jumbo transport vessels.
Technical parameters
- Standard transport capacity: 2 - 150 t/h
- Standard transport distance: 10 - 1000 m horizontal
- Standard vertical lifting height: 10 - 80 m
Advantages of the application:
The equipment can be operated in wide operating range. Main operating parameters of working point belonging to quantitative and qualitative changes of the material to be transported can be changed, resp., adjusted flexibly.
Low power consumption and operating cost.
With PLC control, full automatic operation of the transport equipment of transport vessel can be realized. Because of the low delivery air demand, on venting of the receiving silos we need filters of smaller size compared to the conventional, thin-phase flow pneumatic transport equipment.
Additional advantages against vacuum type systems in case of big fly ash quantities: The fly ash is collected in the transporting vessel, therefore ESP hoppers have no storage function, consequently the plugging of hopper outlet is eliminated.
Several transport vessels can be connected to a common pipeline, thereby a possibility is afforded to construct more complex systems as well.
The most frequent application fields:
- Fly ash transportation in pulverized coal fired power stations.
- Fly ash, bed ash, limestone & sand transportation for fluid bed boilers.
- Transportation of cement and clinker dust in cement works.
- Transportation of foundry sand.
- Transportation of dusty materials in chemical-, food industry and agricultural plants, as well as in pharmaceutical factories.
Combination of airslides and pressure vessel system
For power plants over 300 MW where big size ESP-s with large number of hoppers are required and silos are far from units there is an alternative solution to individual pressure vessels. This is combination of airslides and pressure vessels.
A typical 600 MW unit with two ESP including 32 NOS of collecting hoppers each working as follows:
- From the four hoppers belong to one path, fly ash is conveyed by airslide into big size conveying vessels instead of 4 NOS of smaller ones. Resulting eight (8) pressure vessels instead of thirty-two (32).
- Out of the total eight (8) pressure vessels two (2) or four (4) can even receive boiler ash via short distance pneumatic conveying, making easier to transport the boiler ash to long distance by mixing it with the finer fly ash from ESP.
- Moreover four pneumatic conveying vessels belong to one ESP can be connected to one common ash conveying line in such a way that two-two vessels can be coupled and connected to one common ash outlet valve forming conveying pairs.
Back to top
|